EPS foam is widely used in all walks of life because of its thermal insulation, anti-seismic, and anti-fall characteristics, often named Styrofoam/ Polystyrene. The material often appears in our life in the form of furniture packaging, fish boxes, construction material, EPS leftover, EPS trays, and so on. Styrofoam is no-biodegradable.
The biggest problem with Styrofoam are light in weight, and huge in size. Scattered EPS has difficulty in transportation. Recycling waste Styrofoam can avoid the pollution of the environment, save resources, and offer convenience for Styrofoam material transportation.
EPS Foam Recycling Solution
According to a survey on the recycling of Styrofoam in the United States, the overall recovery data of Styrofoam in the United States is on the rise in recent years, and there are 113.8 million pools recycled in 2018. It can be seen that more and more people begin to pay attention to Styrofoam recycling.
GREENMAX compactor specializes in compressing all kinds of EPS material and can help you to reduce the volume of EPS waste up to 50:1. Its operation process consists of four parts: putting Styrofoam, crushing, cold-pressing, and discharging, which is automatic and not complicated. It is not only easy to operate but also can reduce the volume of Styrofoam by up to 2% and foam pressed ingots, which can be sold to recyclers or be purchased back by GREENMAX.
GREENMAX Foam Compactor Aoplo SERIES:
GREENMAX foam compactor A-C100 has a capacity of 100 kg/hGREENMAX foam compactor A-C200 has a capacity of 200 kg/h
GREENMAX foam compactor A-C300 has a capacity of 300 kg /h
REENMAX Foam Compactor Recycling Steps:
1. Throw the EPS foam to be processed into the hopper—Feed EPS foam into the hopper for Crushing.2. The large EPS foam is Crushed into small pieces.
3. Compaction of crushed EPS foam by pressing technology—Compressing EPS foam by pressing and hydraulic technology.
4. Pressed ingots compacted by screw extrusion.
GREENMAX EPS Foam Compactor Functions:
1. Crushing the waste EPS foam and compact into tight block with 50:1 compression ratio, which saves warehouse space.2. After compressing, EPS Foam can be sold for reusing and making frame products and construction moldings, such as crown molding, wall panel, etc.
3. Avoiding more waste EPS foam being landfilled or burned.
4. Protect the environment, improve environmental condition and save raw materials to reduce the energy crisis pressure.
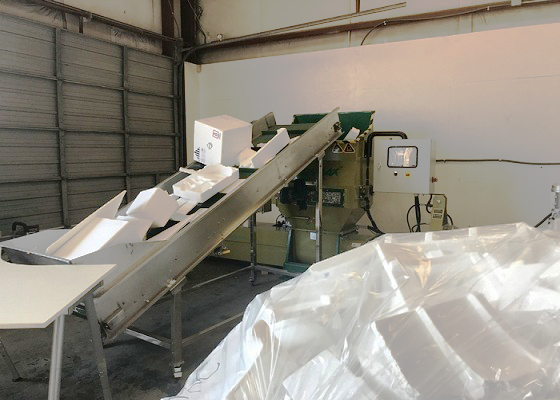
GREENMAX Foam Compactor Advantages :
1. GREENMAX are manufacturing many models with different outputs.
2. The machine can be designed as your requirement.
3. GREENMAX provides after-service in time, there are local engineers ready for support.
EPS Recycling Successful Cases:
The following is a successful case that shows our foam recycling machine are good to use after the logistics company uses the machine. They introduce our machines to others. So now we have some customers who are introduced by our former customers.
CASE 1: Government & Styrofoam Recycling
Oregon county realized that Styrofoam recycling is very important and necessary 4 years ago, the reason they started to consider this recycling project because they got much feedback from residents that it’s urgent to start Styrofoam recycling, and their solution at that time is the only landfill, they think landfill is not healthy and looking for a better solution.
In 2016, Oregon county installed the Styrofoam compactor machine and put it on a truck to make it movable. They drive the compactor around to tell more and more people Styrofoam is recyclable, the residents can drop it there for recycling. Till now, Oregon county has finished around 220,000lbs Styrofoam recycling, their effect is not only focused on this recycling volume, their great job is setting an example for all governments around the states.
CASE 2: Retailer & Styrofoam Packaging Recycling
LOWE’S is a very large retailer, with 700 stores around the states. Normally all stuff is transferred from Distribution Center, at first, all their Styrofoam packaging throwing into the dumpster for landfill, as the business is growing larger and larger, Styrofoam scrap is becoming much more, meantime landfill cost is increasing, and the management found they should find another way to recycle, one side for cost-saving, bring profit, the other hand is also for the company image.
Till now, LOWE’S has finished their budget, they installed GREENMAX Styrofoam compactor in all their DCs, no longer throw away, because their volume is really very large, not only saving a lot of landfill cost, also bring considerable profit, in one year, they recycle at least 25,000lbs. As a famous company, they are standing in front line for recycling.
CASE 3: EPS Manufacturer & EPS foam leftover
As a global packaging solutions leader, SONOCO is manufacturing all kinds of packaging to improve customer’s life, EPS foam is a necessary packaging, SONOCO are running several manufacturing plants to make EPS foam coolers and other molded products. Their production line is equipped with high-level equipment, not generating that much EPS foam scrap, they used to landfill this scrap, while SONOCO has a very professional recycling team is taking care of all the scrap, working to find out a better solution rather than throwing it away easily.
At present, the recycling team started to work with the factory about waste EPS foam recycling, after comparing several different offers, they installed GREENMAX EPS foam compactor in their Hayward location for their waste coolers recycling, after compression, the blocks are transported to the INTCO factory for reusing to make picture frames. Other locations also plan to study this recycling solution and improve their recycling rate.
CASE 4: Fish Company & Fish Boxes Recycling
BluGlacier is a professional seafood company especially salmon, they are the producer of top-quality salmon in Chile for the U.S. With a factory in Florida and Chile, they are running a big fishing company, in Chile, they use Styrofoam boxes for fresh Salmon, their business is very large, so generate a lot of foam boxes. In Florida, they are running a repack company, also generate a lot of boxes.
Recently, they met them in Boston Seafood Show and learned the recycling solution how to recycle their waste Styrofoam fish boxes, it’s a 100% total solution from the recycling equipment, to the end of material purchase-back. They started this recycling project from their Florida factory, after 1 year, they installed another GREENMAX Styrofoam compactor in their Chile factory. Before they know the GREENMAX recycling solution, they have no idea other than landfill. Especially in their Chile location, there are at least 4 truckloads compacted Styrofoam monthly.
GREENMAX Styrofoam Recycling System Models
GREENMAX Foam Compactor A-C100Throughput: 100kg/h
Compression Ratio: 50:1
Compressed Density: 200-400kg/m3
Total Power Consumption: 10.25kw
A-C100 Video:
Throughput: 200kg/h
Compression Ratio: 50:1
Compressed Density: 200-400kg/m3
Total Power Consumption: 19.55kw
A-C200 Video:
Throughput 300kg/h
Compression Ratio: 50:1
Compressed Density: 200-400kg/m3
A-C300 Video: